APD is the fastest wafer dicing provider globally, offering unmatched quick-turn services for all wafer sizes, including 200mm and 300mm. We specialize in dicing Silicon, Gallium Arsenide (GaAs), Silicon Carbide (SiC), Sapphire, Ceramic, Glass, Quartz, Printed Circuit Boards (PCBs) made from FR-4 and various PCB substrates, as well as a wide range of hard and brittle materials. Our standard turnaround is 3-5 days, with options for 48-hour, 24-hour or even same-day service. For urgent needs, some jobs can be completed while you wait in our lobby. We ensure precision and speed to meet your most demanding deadlines.
What is wafer dicing?
The technique of separating individual dies from a larger piece of semiconductor material (a wafer) is known as Wafer Dicing (also known as wafer scribing, wafer cutting or die singulation). This term was created in the semiconductor industry to describe singulation of the individual die from the wafer.
Over the years, the APD dicing processes have evolved into something much broader that no longer fits the simple Wikipedia definition. Although we continue to process semiconductor wafers as our primary bread-and-butter product, a more precise categorization might be precision micromachining of hard, brittle materials.
Customer
Engagement
Process
The most requested wafer dicing process involves the dicing of silicon wafers and is performed by most wafer dicing companies. The APD engagement process is described below. This process can handle the dicing of silicon wafers and is flexible enough to include a broad range of precision manufacturing projects.
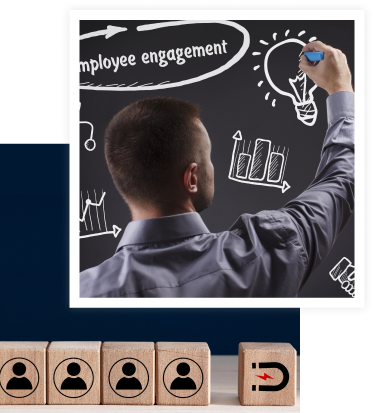
- Project Communication: Communicate project details via email or phone.
- Quote and Material Shipment: APD generates a quote, customer accepts it, and ships material to us.
- Material Inspection: Receive and inspect material, contacting the customer if issues arise.
- Production Documentation: Create documentation and send it to the production floor.
- Production Process: Production manager reviews requirements, creates a plan, and will occasionally contact the customer.
- Wafer Processing:
Wafer undergoes surface protection (if needed), mounting, dicing, washing, QA inspection, packaging, and shipping. And the invoice is sent to the customer.
Customer Service
APD has provided exceptional wafer dicing services since 1999. Our experienced team, many with decades of tenure, ensures quality and reliability. The loyalty of our long-term customers speaks to our commitment to excellence.